
PUROXEN rigid foam systems
To produce rigid foam, two components are used to create the Puroxen system, which has a wide range of applications. After mixing components A and B, foaming occurs. This results in foams that differ in application: pourable, refrigeration, block, insulation, or structural foams. Their preparation involves using pour-in, low-pressure, or high-pressure equipment.
Components of the Puroxen system
Puroxen is typically a two-component system, which gives it an advantage over solutions where the components are already combined. Component A is a mixture of polyols, while Component B is a cross-linking isocyanate. After mixing, a foaming reaction occurs, which can increase the foam volume by up to 100 times. Controlling the temperature of the components and the mold allows for influence over the reactivity of the system. Additionally, the components of the mixture and their proportions affect the properties of the resulting foam.
The first component is known as the polyol blend. It consists of polyester and polyether polyols, flame retardants, catalysts, blowing agents, and surfactants. The second component is polyisocyanate. Their mixing initiates the foaming processes. Depending on the polyols, blowing agents, and surfactants used, either open-cell or closed-cell foam is produced. If a larger amount of pMDI (the cross-linking agent) and appropriate catalysts are involved in the reaction, polyisocyanurate foam will be created.
Applications of pour-in rigid foams
Puroxen systems are used in the continuous and periodic production of closed-cell PIR rigid pourable foam boards. Additionally, a variety of prefabricated products are made from them, such as pre-insulated pipes and insulation jackets. The type of application primarily results from the dominant role of polyisocyanurate bonds, which give the pourable foam its higher thermal resistance.
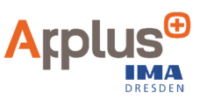
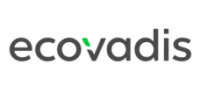
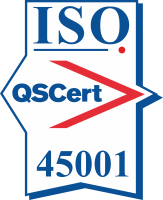
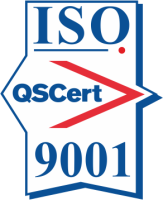
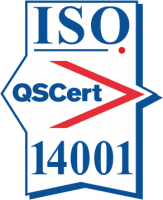